Abnormale Teileverarbeitung!!! Anwendungsbeispiel für die RCA-Root-Cause-Analyse
Was ist eine Ursachenanalyse?
Root Cause Analysis (RCA), auch als RCA-Analyse oder Root-and-Cause-Analyse bezeichnet, ist ein strukturierter Ansatz, der verwendet wird, um die zugrunde liegenden Ursachen für Probleme in Fertigungsprozessen zu ermitteln. RCA geht über die oberflächliche Problemlösung hinaus und zielt darauf ab, Probleme an ihrem Kern anzugehen. Das Konzept der Grundursache dreht sich um das Verständnis der grundlegenden Ursache des Ursprungs eines Problems. In Branchen wie der Maschinenbauindustrie, in denen Effizienz und Qualität oberste Priorität haben, spielt RCA eine entscheidende Rolle bei der Förderung kontinuierlicher Verbesserungen. Durch die Konzentration auf die Identifizierung der Grundursachen ermöglicht RCA Herstellern die Implementierung maßgeschneiderter Lösungen, die das Wiederauftreten von Problemen reduzieren und die allgemeinen Fertigungsstandards erhöhen.
Gängige Methoden zur Ursachenanalyse
- 5 Warums (auch bekannt als Fünf Warums): Dabei wird wiederholt nach dem „Warum“ gefragt, um tief in die Wurzel des Problems einzudringen. Die 5-Warums-Grundursachenanalyse ist eine einfache, aber wirkungsvolle Technik.
- Fischgräten-Diagramm (Ishikawa-Diagramm): Diese Methode, auch Fischgräten-Analyse genannt, kategorisiert potenzielle Problemursachen visuell und deckt dabei Aspekte wie Personal, Prozesse, Materialien und Umgebung ab.
- 4M1E-Methode: Analysiert Probleme umfassend aus fünf Blickwinkeln – Mensch, Maschine, Material, Methode und Umgebung.
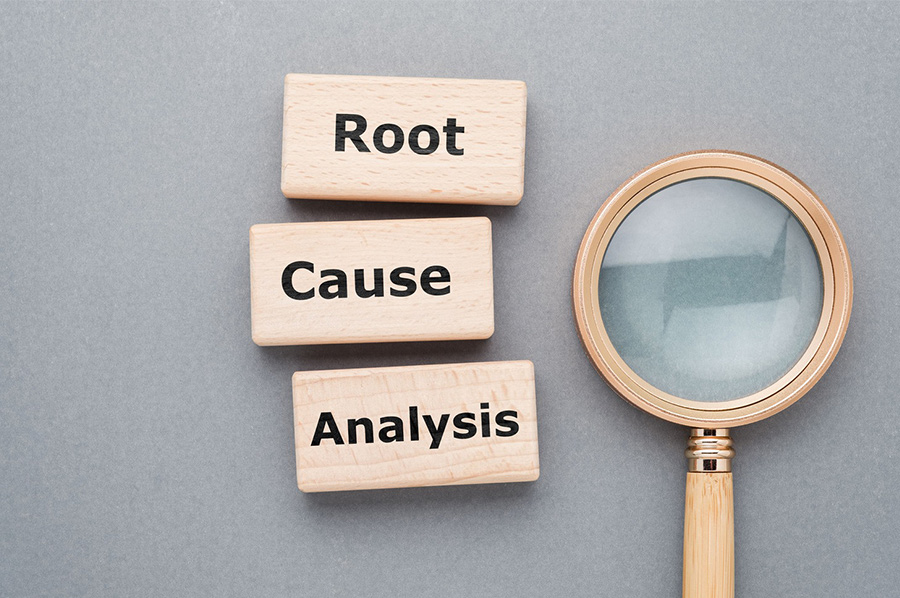
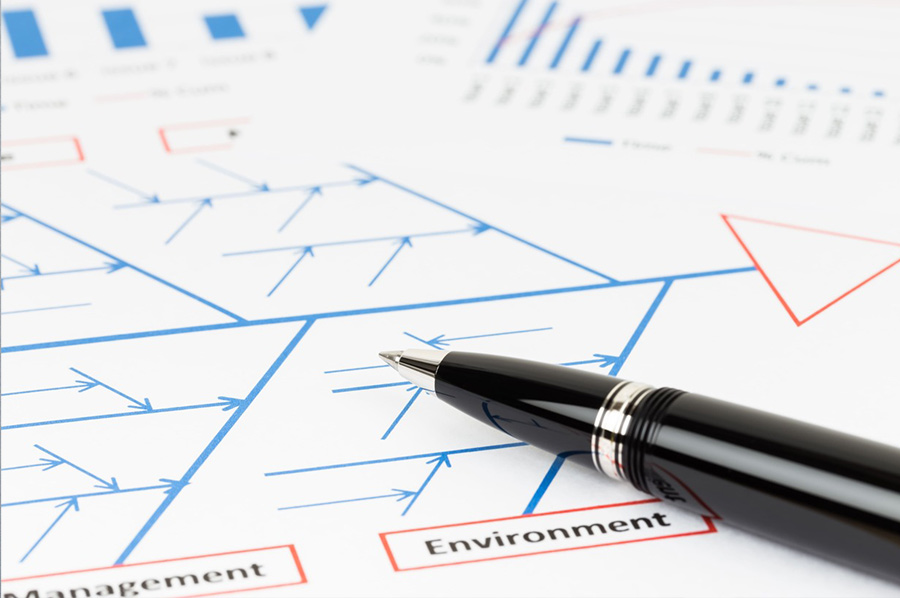
Der Prozess der Ursachenanalyse
Die Methodik zur Ursachenanalyse umfasst typischerweise fünf Schritte:
- Problem identifizieren: Definieren Sie das Problem klar und beurteilen Sie seine Auswirkungen auf die Produktion.
- Datenerfassung: Sammeln Sie umfassende Daten aus Quellen wie Geräteprotokollen, Qualitätskontrollberichten und Mitarbeiterfeedback.
- Identifizieren Sie potenzielle Faktoren: Verwenden Sie Techniken wie die 5 Warums oder die Fischgrätenanalyse, um verschiedene Möglichkeiten zu erkunden.
- Grundursachen ermitteln: Führen Sie eine eingehende Analyse der identifizierten Faktoren durch, ggf. einschließlich Hypothesentests. Dieser Schritt ist für die Identifizierung der Grundursache von entscheidender Bedeutung.
- Lösungen implementieren: Entwickeln und implementieren Sie Lösungen, die auf die Grundursachen abzielen.
Durch Befolgen dieses systematischen Ansatzes können Fertigungsteams Probleme in ihren Prozessen effektiv lösen und so die Effizienz und Qualität der Fertigung verbessern.
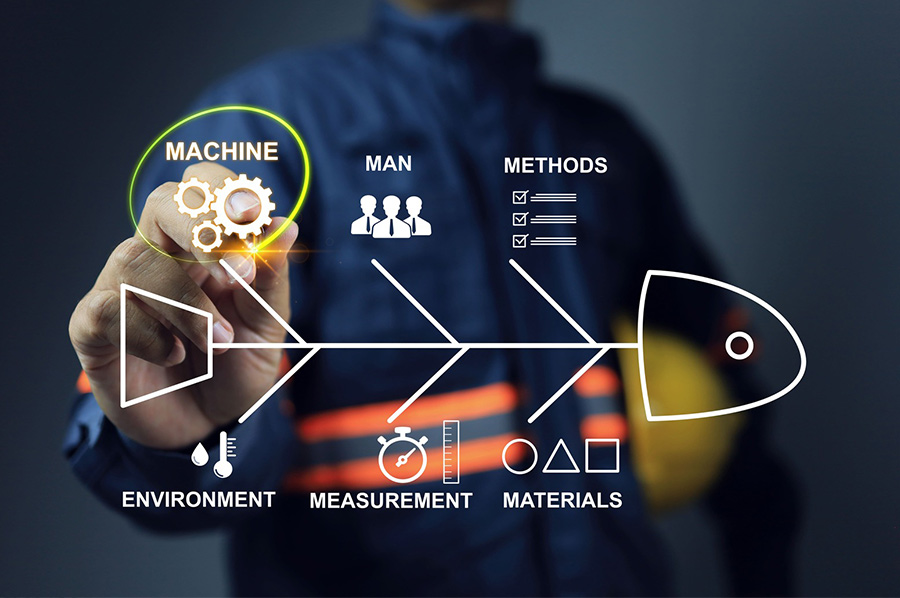
Anwendungen zur Ursachenanalyse in der Bearbeitung
WKPT entdeckte während eines Bearbeitungsprozesses abnormale Werkzeugvibrationen und leitete sofort eine Ursachenanalyse ein. Das Team verwendete die 4M1E-Methode, um die Ursachen des Problems umfassend zu untersuchen. Dies ist eines von vielen Beispielen für Ursachenanalysen im Fertigungssektor. Basierend auf den Untersuchungsergebnissen entwarf und implementierte das Unternehmen eine Komplettlösung:
- Mann: Entwickelte spezielle Schulungsprogramme für Bediener, Verpackungspersonal und Qualitätsprüfer, um ihre Fähigkeit zu verbessern, Probleme mit Werkzeugvibrationen zu erkennen und darauf zu reagieren.
- Maschine: Erstellung eines detaillierten Plans zur regelmäßigen Wartung der Ausrüstung, der sich insbesondere auf den Zustand der Revolverpräzision, des Hydrauliksystems und des Klemmmechanismus konzentriert.
- Methode: Überarbeitete Prozessdokumente, Einbeziehung spezifischer Vibrationskontrollen in wichtige Anweisungen und Inspektionsformulare, um in jeder Phase klare Inspektionskriterien sicherzustellen.
- Material: Bei Form- und Leitungswechseln wurden gründlichere Reinigungsverfahren eingeführt, um Rückstände zu reduzieren, die Vibrationen verursachen könnten.
- Umgebung: Ausgestattetes Qualitätssicherungspersonal (QA) mit Endoskopen für detailliertere Schnittspurprüfungen.
Durch die Implementierung der 4M1E-Ursachenanalysemethode und entsprechender Verbesserungsmaßnahmen konnte WKPT nicht nur das Wiederauftreten von Werkzeugvibrationsproblemen verhindern, sondern auch die allgemeine Bearbeitungspräzision und Produktqualität verbessern. Diese Anwendung der Ursachenanalyse demonstrierte die systematische Problemlösungsfähigkeit von WKPT bei Fertigungsherausforderungen.
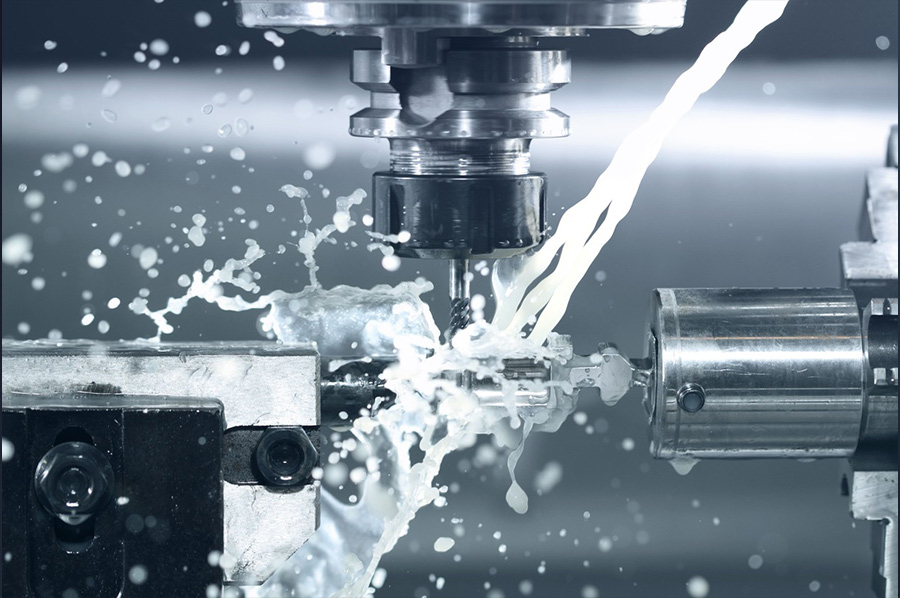
Abschluss
Die Ursachenanalyse (RCA) spielt eine entscheidende Rolle bei der Problemlösung in der Fertigungsindustrie. Durch die Verwendung strukturierter Ansätze wie den 5 Warums, dem Fischgrätendiagramm und 4M1E können Unternehmen die Ursachen von Problemen gründlich untersuchen, anstatt nur oberflächliche Symptome zu behandeln. Die Erfolgsgeschichte von WKPT zeigt, wie sich die RCA in realen Szenarien bewährt. Durch gründliche Analyse und praktische Anpassungen hat das Unternehmen nicht nur das Problem der Werkzeugvibration behoben, sondern auch die Gesamtqualität seines Herstellungsprozesses verbessert. Dadurch konnten wir Ihnen zuverlässigere Produktionsdienstleistungen für Metallkomponenten anbieten..