鑄造技術的發展動向與其特徵
金屬鑄造是一個將高溫液體狀金屬倒進模具空腔內,使其凝固後取出鑄件的製造過程。根據資料調查指出,全球鑄件產量前三大的材質分別為灰口鑄鐵、球墨鑄鐵與鋁,合計占了85%的比例,其中灰口鑄鐵加球墨鑄鐵就有71%的比例,顯示鑄鐵件市場需求仍屬大宗。
砂型鑄造的技術應用廣泛,也是最早問世的鑄造技術,至今仍是生產鑄鐵件的主要技術。以沙子作為模型的成本相對低,在鑄件尺寸、數量與成本考量的條件下,砂鑄是適合的鑄造方案。。
使用砂模鑄造工法,在取出鑄件時需要破壞供一次性使用的砂模,日後再重新製作。當鑄件需求量眾多時,使用永久性的金屬模反而會更節省成本。 金屬模即是使用金屬作為模型, 可以多次重複使用,適合中小型零件的大量生產。金屬模的常見鑄造工法有壓鑄與重鑄。壓鑄是使用壓力,把熔融的金屬壓入金屬模的鑄造工法;重力鑄造則不使用外在壓力,靠金屬本身的重量自行成型。
金屬模解決了一次性使用與大量生產的問題,不過熔融金屬流動不良與氣孔引起的鑄造缺陷仍需後續新的鑄造工法解決。
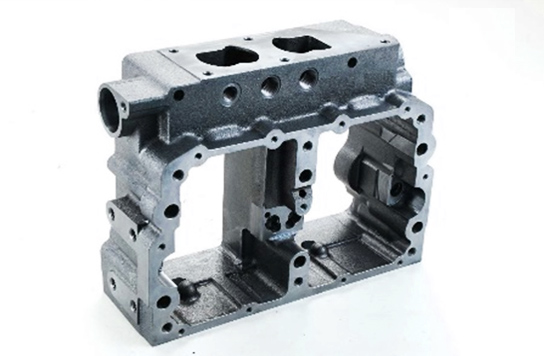
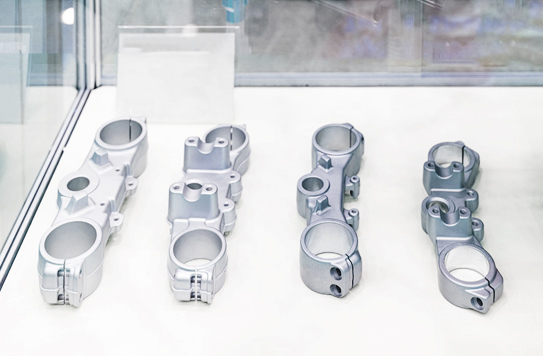
在重視鑄件品質的前提下,新鑄造工法開始出現,試圖解決因流動不良引起的鑄造缺陷,各式改良鑄造技術例如:
- 進真空壓鑄:在模具裝上抽氣裝置,把模具內的空氣先行抽走,減少空氣引起的氣孔。
- 層流壓鑄:改變壓鑄原有的高速充填,改以低速進行,減少充填過程捲入的空氣。
- PF壓鑄(Pore free Casting):又稱無孔壓鑄、充氧壓鑄,在模型內注入氧氣再行充填,是另一種減少充填過程中捲入空氣的工法。
- GF壓鑄(Gas free Casting):透過模型內的排氣孔,將多餘的空氣排出,也是真空壓鑄的一種方式。
- 擠壓鑄造(Squeeze Casting):結合壓鑄與鍛造的概念,先是以低壓鑄造進行,再施以高壓,從而得到較少鑄缺且高強度的壓鑄件。
上述新型鑄造法均是為了解決流動不良而生,改善程度或多或少,因此又延伸出進化的工法,例如超高速壓鑄、高真空壓鑄、半固態鑄造,分別從速度、抽取空氣與半固態成型的方面再進化。其中半固態鑄造結合鑄造與鍛造的優點,依製程不同又可分為觸變鑄造(Thixocasting)與流變鑄造 (Rheocasting)。
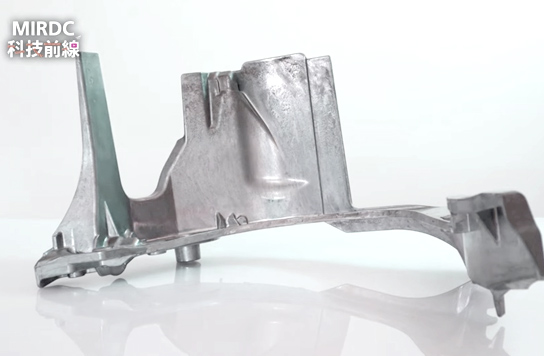
鑄造技術發展以來,在既有的技術基礎改良外,往更極致的方向延伸,例如材料或一體化成型的技術,讓鑄造技術更進一步。目前的技術發展如下: 微細化技術:鑄件常見的缺陷有縮孔跟氣孔,這兩種缺陷除了從上述不同的鑄造技術加以改善外,也可從鑄件晶粒著手。細晶鑄造技術就是透過控制鑄造參數、或以機械外力、或以添加細晶劑,其目的都是讓鑄件晶粒微細化,達到機械性質提升的效果。
一體化成型(gigacasting):一體式壓鑄自從特斯拉開啟應用以來,其他車廠也開始投資這項技術。一體化成型在汽車產業的應用,除了提高生產效率以外,也簡化了生產流程與零組件。
非熱處理高強度/高延性材料:大多數壓鑄鋁合金使用 ADC12,材料特性是容易加工,但其合金組成讓它即使用高品質壓鑄法,仍無法達到高韌性需求。為解決此限制,高強度高延性的材料 Al-Mg-Si 系壓鑄合金因應而生,不須經過熱處理也具備高強度高延性的機械性質。
鑄造技術問世以來,從成本優勢到提升品質,再到永續發展減少浪費,技術走向降低生產成本與提升鑄件品質的方向發展。光隆精密工業以廠內成熟的砂模鑄造技術,輔以 DISA 自動化造模與 MAGMA 軟體輔助分析,加上高強度 ADI 材料的開發,使鑄鐵件在交通運輸、建築機械、農業機械等領域開展應用。在非鐵金屬的鑄造應用上,光隆精密工業能以多元的供應鏈資源,提供鋁合金重鑄、壓鑄、精密鑄造等機械零件,在航空、醫療器材與高精密電子設備應用取得實績。除金屬成型以外,再加上機械加工與表面處理製程,即是光隆精密工業為各產業應用的機械零組件OEM製造方案。
參考資料
板村正行(2024年3月)。高品質(スクイズ・真空・半凝固)ダイカスト法の開発。「脱炭素・AL時代のSDGsに向けて」研討會發表之專題演講,台中長榮桂冠酒店。
薛乃綺(2024)。汽車製造工藝新篇章:一體式壓鑄底盤的應用與挑戰。
蔡佳彣(2019)。探討全球非鐵鑄造市場發展趨勢。
曾婉如(2015)。2014年全球鑄造產業市場現況回顧。
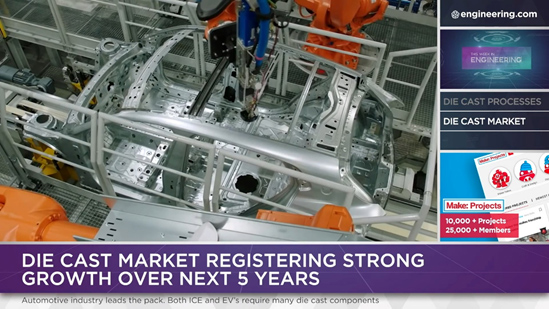