光隆精密工業は、プロセスのアップグレードを通じて炭素削減を達成し、グローバルグリーン・サプライチェーンの要件に準拠
グローバルトレンドは、環境保護が普遍的な価値となり、世界中の国々がエネルギーの節約と炭素削減の重要性を認識していることを示しています。グローバルなグリーン・サプライチェーンへの需要に対応するために、国際的な炭素排出に関する規制が徐々に整備されています。グローバルなサプライチェーンの要件に適応するため、光隆精密工業は2023年に「自動車部品のスマート製造による生産プロセスのアップグレード」プロジェクトを開始しました。このプロジェクトは、工作機械でのネットワーキング技術の適用を向上させることを目指しています。プロセス最適化を通じて、部品製造プロセスの分析を支援し、処理中に発生する潜在的な炭素排出を予測するために炭素排出モデルを活用しています。
光隆精密工業は、切削プロセスに従った力学シミュレーションを使用して、ツール経路上の各ポイントでパラメータを推定します。これには切りくず厚さ、切削力、スピンドル負荷、ツール負荷が含まれます。シミュレーション結果とユーザーが定義した条件制限に基づいて、送り速度は主軸、ツール、ワークピースを効果的に保護するために調整されます。
光隆精密工業は特定の条件下で切削の加工力を活用しています。最大切りくず厚さ、横方向の切削抵抗、軸方向の切削抵抗、主軸トルク、エアカットの最適化どのパラメータを設定し、条件制限に基づいて最適な切削フィード効率を調整します。切削力学の解析モジュールを使用してさらなる最適化を行い、加工プログラムを診断し、送り速度を修正して、最終的には最適化された加工プログラムが生成されます。このプロセスにより、加工効率が向上し、炭素排出が低減し、主軸、ツール、そしてワークピースが保護される効果が得られます。
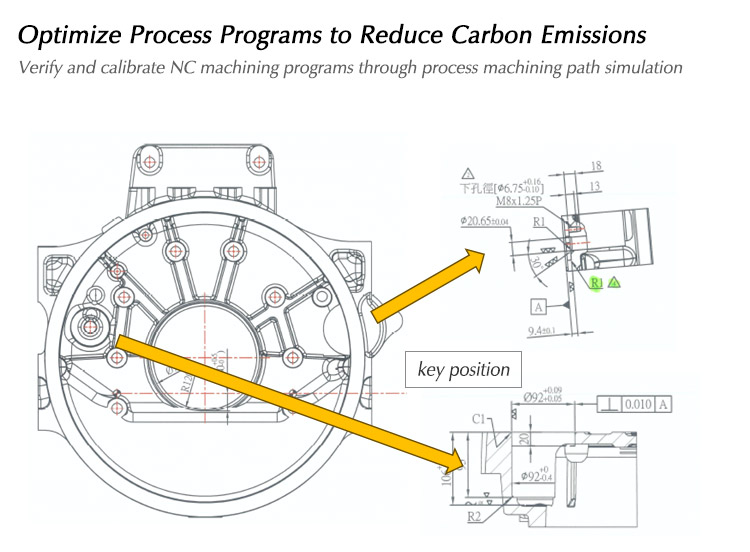
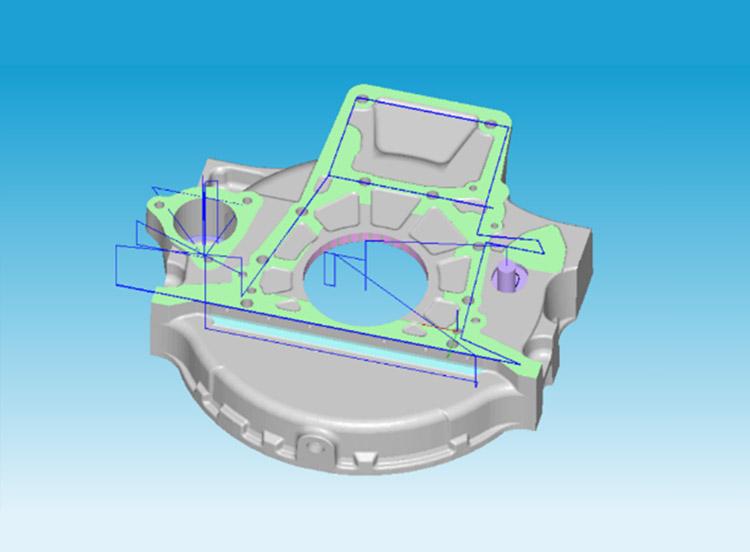
光隆精密工業のプロセス最適化は、力学の解析に基づいています。これは、フライス加工プロセスの最適化に使用される工程、ワークピース、機械の分析を含み、材料の除去によるツールへの力を計算します。加工経路、ワークピース、機械などの条件に基づいて、最適な送り速度を設定し、切削効率を向上させ、無駄な電力消費を削減し、それにより加工時間を節約し、炭素排出を低減します。具体的な手順は以下の通りです:
- 加工経路のシミュレーションを行い、切りくずの厚さや切削力などのデータを推定します。
- NC加工プログラムを検査と校正し、加工の精度を確保します。
- 3Dシミュレーションソフトを使用して、材料の除去後の最終形状を検査します。
- 切削力学のシミュレーション結果に基づいて切削パラメータを設定します。
- 切削力学の解析モジュールを使用してさらなる最適化を行い、加工の送り速度を調整します。
- 最適化された加工プログラムを生成します。
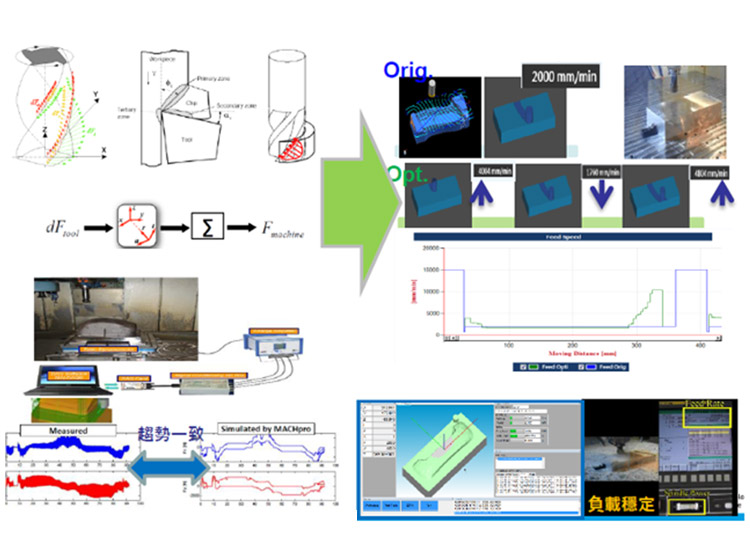
自動車部品の製造プロセスにおける切削力学のシミュレーションにおいて、光隆精密工業は刀具経路上の各ポイントでの切りくずの厚さ、切削力、スピンドル負荷、ツール負荷を推定します。一部の負荷が低すぎるNCプログラムに対して、送り速度を調整して負荷を増加させ、最適化と製造効率の向上を達成します。同時に、切りくず負荷の増加を調整し、横向きの負荷を制限するとともに、受力状況に基づいて切削送り速度を調整して切削効率を向上させる目標を達成します。
実践を通じて、光隆精密工業の最適化されたプロセスは加工時間を5-30%節約し、電力消費を約0.8-4.7度削減し、炭素排出を約6.78%減少させ、同時に生産効率を19.52%向上させました。光隆精密工業は国際サプライチェーンの要件を満たすだけでなく、環境の持続可能性へのコミットメントを示しています。
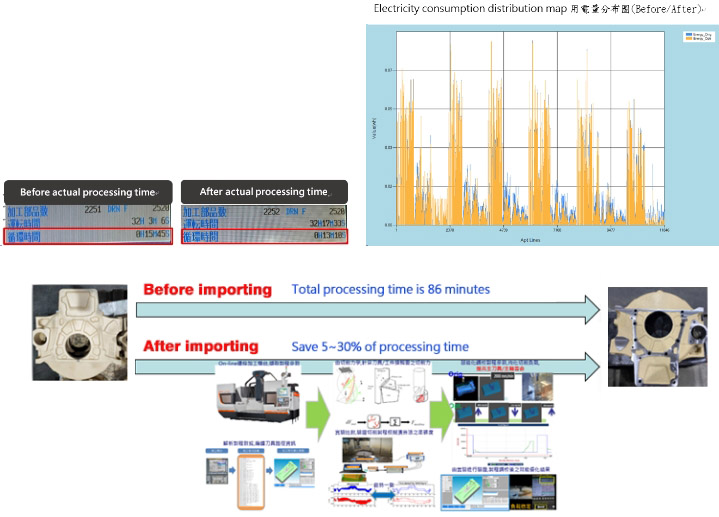