Custom Tooling & Mold Development for High-Volume Manufacturing
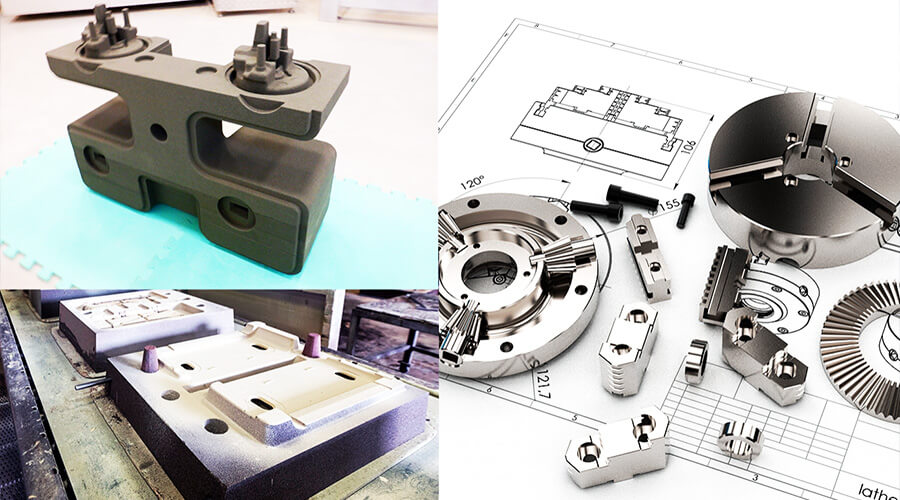
The forming of parts mainly goes through two different processes. The first process is to shape the metal material through a variety of molds, generally in rolling, casting, forging, extrusion, drawing, stamping, etc., and the tool for shaping the metal material is called a mold. The types of forming molds provided by WKPT are: extrusion molds, pressure casting molds, gravity casting molds, sand casting molds, hot and cold forging molds, stamping molds, etc.
The second process of part forming is to use various tools to do milling, turning, boring, grinding, drilling, etc. on the initially formed workpiece or material block to remove material. In order to ensure that the workpiece can be fixed on the machine during the machining process, the workpiece must be fixed with a clamp. In addition, if the cutting tool meets a non-planar surface, in order to assist the accurate positioning of the tool, a jig will be used as an auxiliary tool for stable cutting.
WKPT is a professional manufacturer of precision metal forming and parts machining. We have dedicated ourselves to developing various parts forming molds for many years, with a complete mods development procedure. In the stage of precision machining, standard operating procedure (SOP) such as quality verification, regular inspection and maintenance will be strictly implemented on development, testing and management of various jigs and fixtures.
-
Metal forming has various processes and types such as casting, forging, extrusion, rolling, drawing, stamping, cutting, powder metallurgy, etc. Among all, the forming mold refers to the tool that allows the molten liquid metal with formability or fluidity to be injected or pressurized into the specified mold during the metal products forming process, and makes the metal into the specified shape. Mold has a specific contour or cavity shape, and the application of the cavity shape can make the metal material get a corresponding three-dimensional shape. Generally, Molds are made of a movable die and a fixed die. When molds are combined, the liquid metal is injected into the mold cavity to be formed, and the workpiece can be taken out when separated.
-
During machining, when a metal workpiece is cut by a tool, the inertial force of the tool and machine will act on the workpiece itself.
In order to keep the workpiece unmoved during the machining, a larger clamping force must be applied to stabilize the workpiece on the machine and absorb the cutting force to complete the cutting. The device that fixes and clamps the workpiece is called a fixture.
Compared with the fixture for a workpiece, the jig is a tool to guide the workpiece.
Especially when cutting on non-planar surfaces, the jig can position the tool precisely and stabilize the cutting. However, the CNC machining fixture of the machine can omit the guiding function of the tool; only the positioning and clamping functions are available.