High Precision Equipment Components & Manufacturing Services
Why Choose WKPT for High Precision Equipment Industry?
WKPT can provide technical manufacturing services for the production and modification of components required by the high-precision equipment industry, assisting Taiwan's electronic component sector to leverage its advantages.
WKPT possesses high-precision equipment and peripheral parts manufacturing capabilities. We specialize in designing precision valve components, pump components, automated transportation equipment components, biomedical electronic inspection equipment components, medical care aids, AI smart aids, and other components through CAD. Additionally, we have reverse engineering capabilities, enabling us to trace back the manufacturing process, structural data, and specifications of products for remanufacturing. This is why you can choose WKPT for forming and machining services for precision equipment components.
Results
Advantage
WKPT integrates internal and external machining resources, providing various metal materials including cast iron, aluminum alloy, stainless steel, and carbon steel. Besides, WKPT employs CNC engineers with process development and programming capabilities, and along with internationally certified quality management systems. The accumulated proven cases in medical and electronics applications can tell that WKPT is capable of high-precision parts manufacturing.
In addition to complete machining techniques, we can utilize casting processes such as gravity casting, die-casting, and investment casting to replace the full cutting process of semi-finished products. By adopting suitable machining processes instead of the original multi-step machining process, we can produce parts with high precision and low surface roughness.
We have obtained ISO 9001:2015 and IATF 16949 quality management system certifications. Our outsourced instrument calibration facility is accredited by the Taiwan Accreditation Foundation (TAF), indicating our ability to provide precise and reliable precision manufacturing services for high-precision equipment components with internationally standardized quality management and measurement standards compliance.
In the manufacturing process of high-precision equipment parts, we have installed pollution control equipment that exceeds environmental regulations to minimize environmental impact. Our factory is equipped with activated carbon adsorption towers to treat exhaust gases and adsorb harmful substances generated during processing. Additionally, we have established a wastewater treatment system and have obtained a water pollution prevention permit.
Our experienced English and Japanese-speaking sales representatives can provide full-service support from high precision equipment parts design to product delivery. With decades of accumulated resources in the machining industry, we can offer competitive prices and lead times advantageous to the high-precision equipment supply chain.
Cases
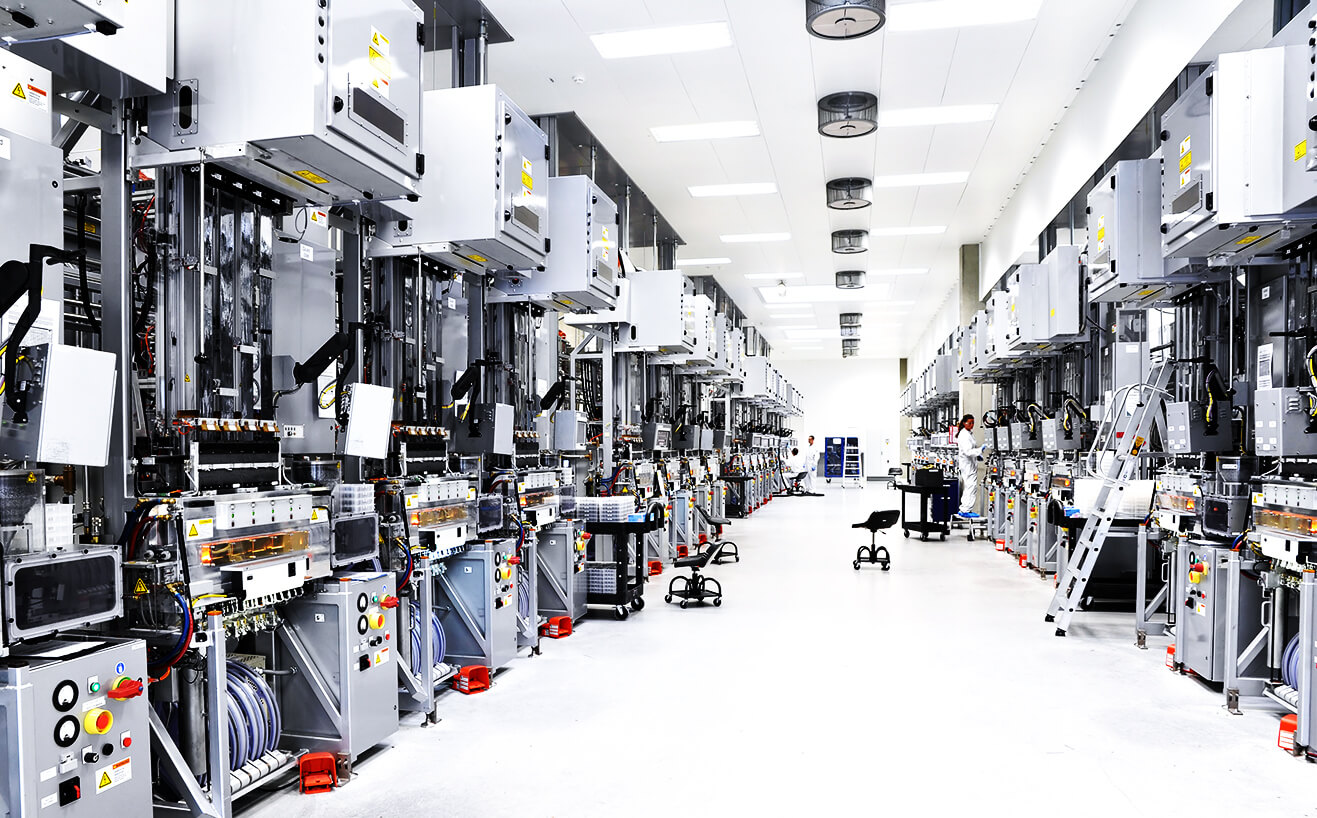
Materials
Aluminum alloy is the general term for aluminum-based alloys. The main alloy elements are copper, silicon, magnesium, zinc, and manganese, and the secondary alloy elements are nickel, iron, titanium, and chromium.
Stainless steel, also known as galvanized iron, is the common name for corrosion-resistant steel. More specifically, steel with chromium (Cr) content greater than 12% in molten steel is called stainless steel.
Carbon steel is an iron alloy with carbon elements, that is, iron-carbon alloy. Carbon steel refers to carbon content higher than 0.02% and lower than 2% (above 2% is called cast iron, and less than 0.02% is called wrought iron).
Manufacturing Capabilities
WKPT is capable of metal forming technologies including gravity casting, die-casting, and investment casting. Materials are covering cast iron, aluminum alloy, stainless steel, and carbon steel. In addition to forming, we also integrate processes such as casting, finishing, precision machining, surface treatment, assembly, and testing, serving as a modern high-precision equipment parts manufacturing facility.
CNC machining is the main method used by WKPT to manufacture high-precision equipment parts, covering the cutting of castings or full cutting of billets, and can be applied to materials such as aluminum alloys, stainless steel, and cast iron. CNC machining is the main business of WKPT, and it is also one of the machining technologies suitable for manufacturing high-precision equipment parts.
High-precision equipment parts often have requirements such as corrosion resistance, no dissolution, high hardness, chemical resistance, and control of heat conduction and thermal expansion coefficient. In addition to the inherent characteristics of the materials themselves, we also provide additional surface treatment services such as coating, electroplating, electroless nickel plating and anodizing to improve high-precision equipment parts to meet the required mechanical properties.
More Resources
-
PCB bracket manufacturing for electronic machinery requires exceptional precision and dimensional stability to support critical printed circuit board assemblies in demanding electronic applications. WKPT specializes in producing aluminum alloy PCB brackets through advanced gravity casting processes, delivering components with superior quality characteristics including stable material properties, high-precision dimensions, and refined surface finish that significantly reduces subsequent machining requirements. Our spindle brackets for PCB punching machines meet stringent specifications with dimensional tolerances under 10μm, shape tolerances under 15μm, and surface roughness below Ra 1.6, ensuring optimal performance in electronic machinery, data communication devices, passive components, printed circuit boards, and electronic tube applications. Through specialized customization capabilities, WKPT manufactures complete bracket assemblies with upper and lower seat configurations, utilizing gravity casting techniques that save both material consumption and processing time while maintaining the exacting standards required for electronic component manufacturing.
-
After multiple tests by the development team, mass production will be begun after the quality is confirmed by the customer. Since the product requires high mechanical properties, including tensile strength and hardness, the manufacturing process is set aluminum alloy blocks for full engraving, which also increases the difficulty of processing and process time. In addition, at least two or more machine tools are used in the manufacturing process for multi-axis machining, and the product size is prone to deviate due to deformation during the cutting process. Therefore, it is necessary to adjust the machining procedure to reserve the machining amount, and refine in the final stage to ensure that the final product meets the requirements of dimensional tolerance and shape tolerance.