Assembly/welding/measurement/packaging services
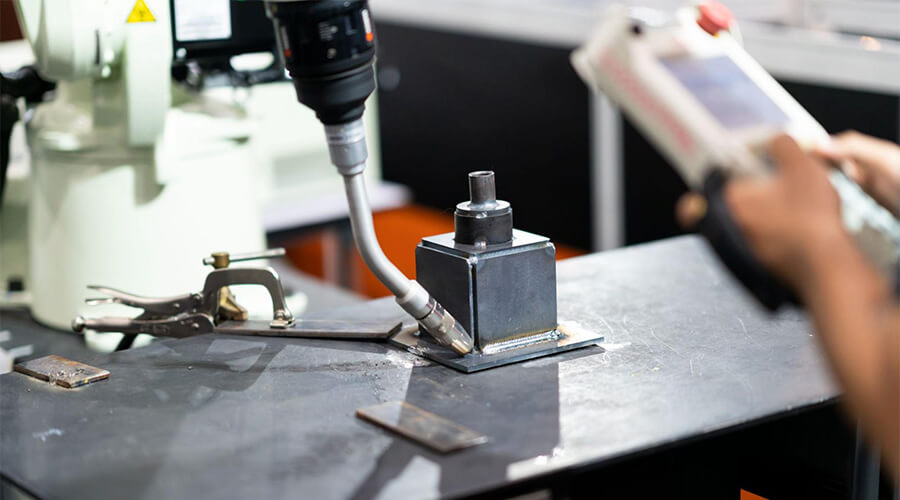
WKPT has integrated metalworking technologies from metal material forming, machining, surface treatment, assembly, welding and functional testing, etc. According to the needs of customized products, there are also corresponding manufacturing processes. In terms of assembly, there are dozens of operations involved, from the initial cleaning and protection to the final packaging. Assembly would be regarded as finished while all operations are implemented correctly on the standard operating procedure.
-
Cleaning
Use ultrasonic cleaning tools to keep clean before and after assembly to avoid product scratches and dirt during assembly. -
Measurement
Check the quality of the assembly line through the IQC to ensure that the materials meet the specifications, and complete quality control before and after assembly. -
Protection
Use packaging material to cover and fill in the assembly process to avoid cuts during assembly, as well as bumps and paint peeling during the final packaging stage.
-
Assembly
Through standard jigs and fixture design to fix the assembly parts. All tools and spare parts also have corresponding part numbers to ensure consistent product assembly quality. Every screw fixing procedure will be locked within the specified torque range. -
Packaging
Move the finished products through a work-saving device for occupational safety of site operators and avoid bumping the products. Packing at a fixed location, and counting the parts and quantities without shortage. -
Final
A label with the number and date on finished products indicating that the assembly is complete. A assembly inspection report will be attached with the goods, which includes the assembly process confirmed item by item, and confirmation by the assembly specialist and the quality assurance specialist.
Welding is a manufacturing process that joins materials, usually metals or thermoplastics, by using high heat
or pressure to melt the parts together and allowing them to cool, causing fusion. Modern welding technology
first appeared at the end of the 19th century, and has developed various welding methods, such as gas
welding, arc welding, laser beam welding, etc. Among the application materials that we often handle, cast
iron is known for its high elongation; while stainless steel is high temperature resistant and
corrosion-resistant.
Different metals have different properties. In response to the customer's product
specification requirements, we can provide welding technology of the same metal material, even between
different materials, which will be closer to the customer's flexible demand for metal material applications.
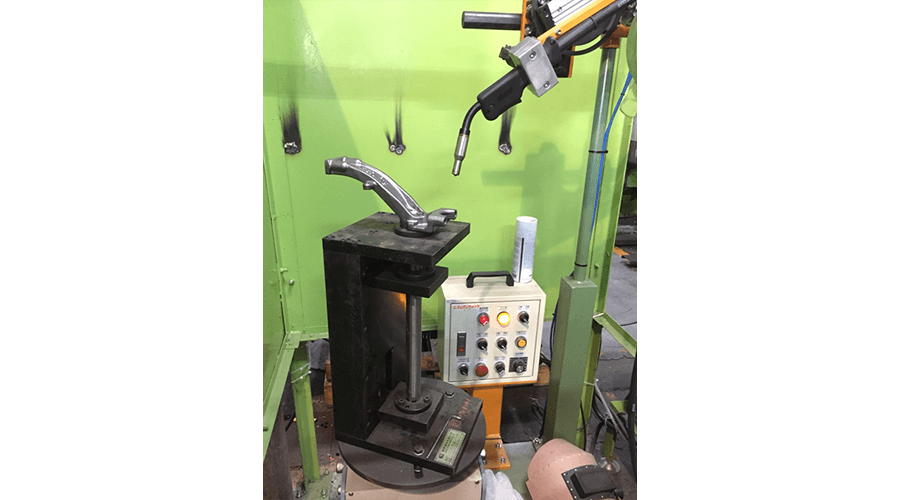
In the welding process, we use the corresponding welding equipment after confirming the specifications of the
product welding. The welding steps are presented in standard operating procedures and executed. The welding
operation will be carried out after confirming that the environment, specifications, parameters, etc. are
all correct. During the welding process, we notice whether there is discontinuity or abnormality to avoid
welding defects caused by discontinuity.
In order to ensure the welding quality, we confirm that the welding quality meets the requirements by
metallographic analysis through destructive testing or external third-party testing.
WKPT’s dedication in the field of metalworking is not limited to front-end machining processes, but extends to assembly and welding in the post-end processes. We are expected to provide more service momentum for the post-process of assembly and welding on our future expansion plan.
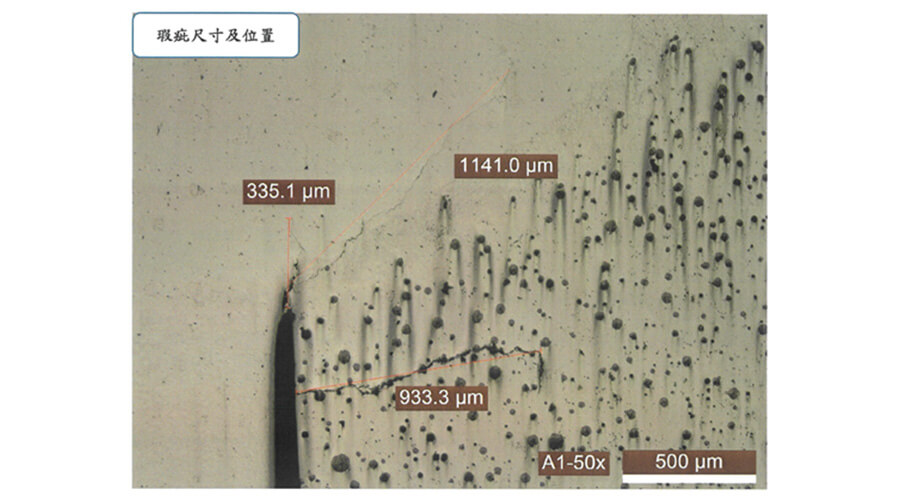