Metal Forming
Benefits of WKPT’s Forming Services
Are you looking for mass production machining services for metal parts? We supply quality-assured metal components under IATF 16949 and ISO 9001 quality management systems. Leveraging advanced lean production and smart manufacturing resources, we efficiently fulfill your entrusted projects. We integrate both in-house and external resources to provide metal component machining services primarily focused on cutting processing, with additional forming processing capabilities. With decades of refined casting experience, coupled with proficiency in mold flow analysis technology, WKPT is your preferred choice for custom metal forming processing.
Forming Results
Forming Capabilities
WKPT has an in-house casting system with capabilities in sand casting and mold flow analysis, providing various material iron casting services.
With a cooperative system equipped with a 1000-ton energy aluminum alloy die casting machine, we offer aluminum alloy die casting services.
With a cooperative system for aluminum alloy gravity casting, we offer aluminum alloy gravity casting services for weights ranging from 5 to 100 kilograms.
With a cooperative system for aluminum alloy investment casting, we provide aluminum alloy investment casting services.
With a cooperative system for aluminum alloy forging, we offer aluminum alloy forging services.
With a cooperative system for aluminum alloy extrusion, we provide aluminum alloy extrusion molding services.
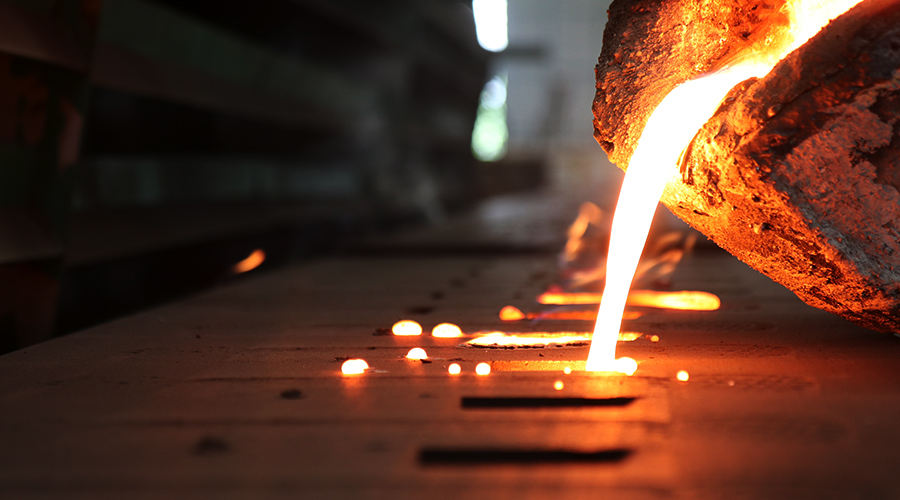
Forming materials
Forming Cases
A qualified hydraulic pump swash plate must meet specifications for surface hardness and compound layer thickness, hole diameter/hole spacing/verticality, and surface roughness requirements. We conduct inspections during the heat treatment and machining processes to ensure the workpiece achieves the required precision. Especially for surface roughness requirements, we integrate the lapping techniques to achieve a smooth surface with an Ra of 0.2µm for cast iron parts and obtained invention patent of it.
The exhaust gas manifold is used in commercial vehicles or heavy machinery and is characterized by high temperatures. Therefore, there are specific requirements for material and hardness. Inspections will be conducted during the incoming material inspection and machining processes to ensure the workpiece achieves the required precision, with a surface roughness (Ra) of less than 1.6µm and dimensional and shape tolerances of less than 15µm. Recommended materials include high-silicon molybdenum ductile iron or gravity casting aluminum alloy, which can meet the high-temperature resistance characteristics required for exhaust gas recirculation manifolds.
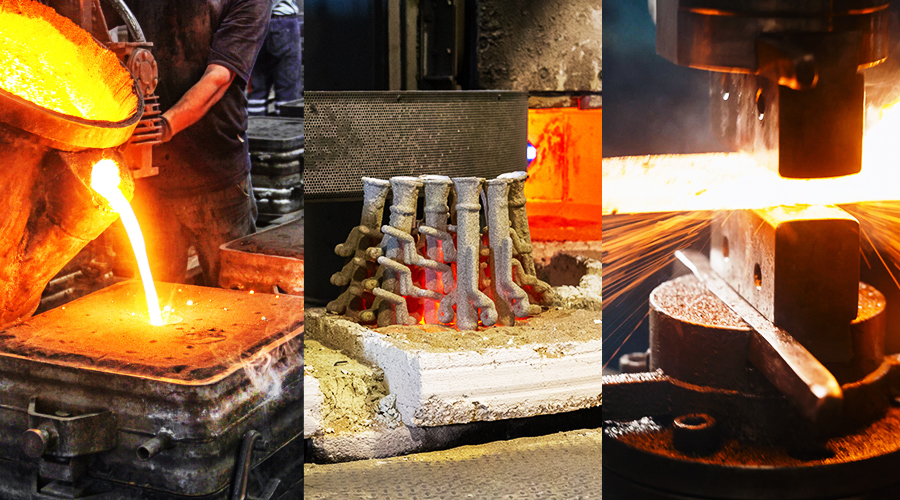
Metal forming is the process of pouring molten metal into molds and shaping it. Common methods of metal forming include:
- Sand casting - Pouring molten metal into sand molds to solidify into shape.
- Die-casting - Injecting molten metal under high pressure into metal molds to shape it.
- Gravity casting - Also known as permanent mold casting, it involves filling metal molds with molten metal using gravity to shape it.
- Lost wax casting - Also known as investment casting, pouring molten metal into wax molds to shape it.
- Forging - Using molds and applying high temperature and pressure to deform aluminum into the desired shape.
- Extrusion - Using molds and applying pressure to force aluminum through openings to shape it.
The choice of forming method depends on the material, the final application of the workpiece, and the quantity of production. WKPT has decades of experience in metal forming and integrates both in-house and external resources to provide a wider range of metal forming services of various materials, creating value for the mass production of metal parts.