Customized brake parts, industrial brake parts
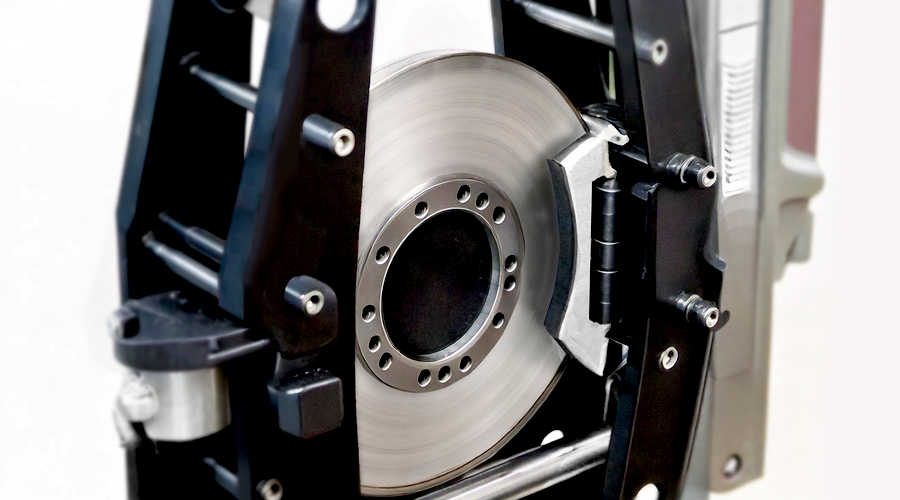
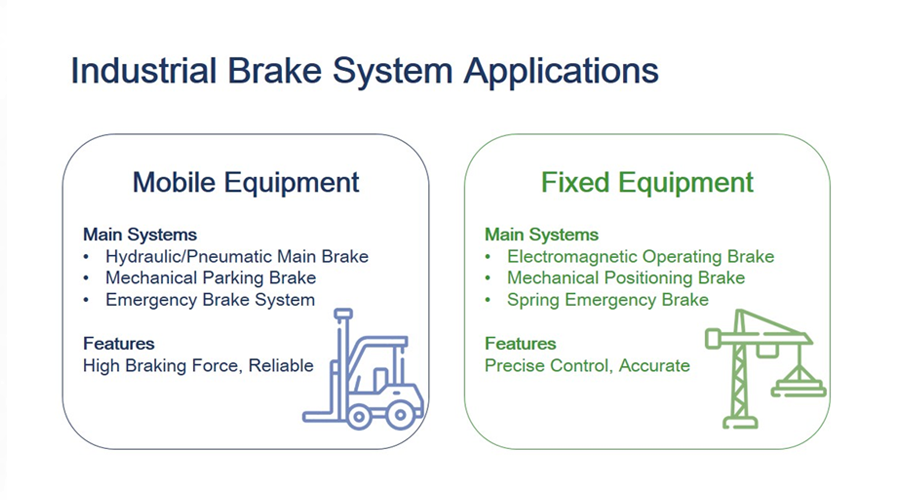
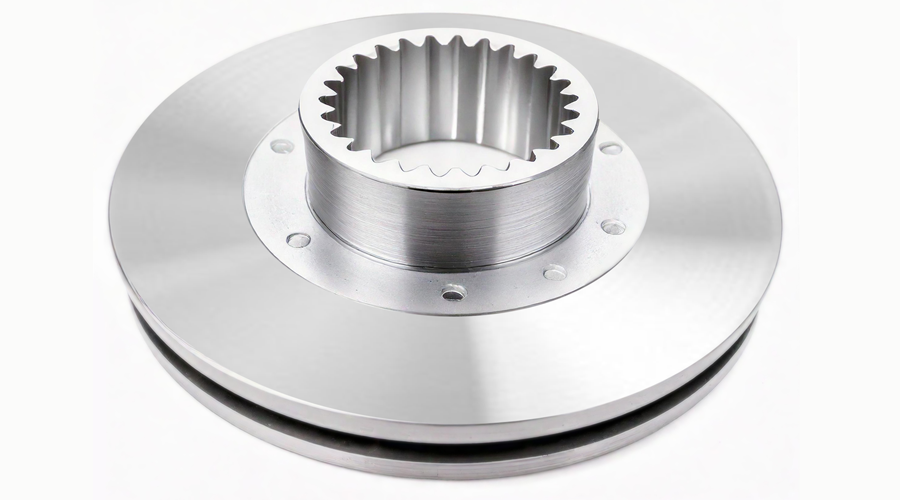
Industrial braking systems are critical safety components in modern equipment. From port cranes to automated production lines, these high-load precision devices require reliable braking systems. Quality brake systems provide emergency stopping power while maintaining production efficiency through precise control. With Industry 4.0 automation, brake system reliability affects both production continuity and worker safety.
Industrial brake systems can be categorized into mobile equipment and stationary equipment according to the application. Mobile equipment, such as forklifts and mining trucks, usually use hydraulic or pneumatic systems as the main brakes, with mechanical parking brakes and emergency braking systems for safety protection. For stationary equipment such as cranes and conveyor belts, electromagnetic brakes are commonly used for daily operation control and mechanical brakes are used for precise positioning with spring brakes for emergency braking. Different applications have different requirements for brake systems, for example, mobile equipment emphasizes braking force and reliability, while stationary equipment emphasizes precise control and positioning capability, so the actual application requirements need to be taken into account when selecting a brake system.
Industrial brake mechanisms are mainly categorized into disc, drum, belt and block types. Disc brakes are often made of ductile iron with specially designed friction discs, which have excellent heat dissipation properties and are suitable for frequent braking, but the braking force varies with temperature. Drum brakes are made of wear-resistant cast iron with self-compressing effect, which can provide large and stable braking torque and good sealing, suitable for operation in harsh environments. Belt brakes utilize flexible brake belts to encircle the drums and are often used when light weight is required. Block brakes are applied directly by means of a rigid pressure block and are suitable for heavy equipment braking requirements.
Two primary cast iron materials are used: gray cast iron (140-410 MPa tensile strength, 150-250 HB hardness) for general applications, and ductile iron (410-830 MPa tensile strength, 170-280 HB hardness) for high-load environments. Selection considers operating temperature, load requirements, service life, and maintenance needs.
Industrial brake system components require high-precision process control, especially when processing key components such as electromagnetic brakes, hydraulic calipers, and drive units. Taking the active clamp braking system for port cranes as an example, the braking surfaces need to be precisely turned and ground, with surface roughness controlled to below Ra 0.8, and heat-treated or mechanically strengthened to enhance wear resistance. For hydraulic disc brakes commonly used in mining equipment, high-precision CNC machining centers are required to maintain the parallelism between brake pad and disc contact surfaces within 0.02mm, which is crucial for stable braking performance. In the machining of complex brake system components such as yaw brake housings, brake drums, and brake pistons, multi-axis machining centers with specialized fixtures are used to precisely control critical dimensions. For wear-resistant parts like brake shoe holders and rotor brakes, sectional machining combined with strict tolerance management is employed to meet assembly precision and operational reliability requirements.
Our comprehensive quality system encompasses material testing, process control, and final inspection. Material testing follows ISO standards for strength, hardness, and composition. Process control monitors dimensions and surface quality. Final inspection verifies functionality and appearance against customer specifications.
Industrial brake systems must withstand extremely harsh environmental tests in practical applications: from high-temperature friction capable of deforming metals, sub-zero temperatures that can make materials brittle, severe corrosive environments filled with salt spray, and intense vibrations caused by repeated impacts. Using high-performance cast iron materials such as GJS-600-3 or EN-GJL-300 can effectively enhance the tensile strength and low-temperature impact resistance of components. In terms of manufacturing processes, heat treatment procedures such as annealing, quenching, and tempering can further optimize the material,s microstructure and improve mechanical properties. Finally, surface treatment technologies provide protection against salt spray corrosion, enhancing the overall durability of components in harsh environments.。
Further reading:Cast Iron Wind Turbine Brake Parts
Further reading:Wind power generation and green energy equipment parts manufacturing
As a reliable partner of your industrial brake system, World Known Precision understands the importance of brake components to the safe operation of your equipment. With our complete manufacturing capabilities from metal forming, precision machining to surface treatment, we are able to provide you with customized, high-precision industrial brake system component solutions. Whether you are a large industrial equipment manufacturer or a professional brake manufacturer, we can provide the most suitable industrial brake system components according to your needs.
With decades of experience in the industry and advanced manufacturing facilities, we have established long-term relationships with major industrial brake and equipment manufacturers, and our products are recognized for their quality and reliability. We are committed to supplying high-quality brake system components that meet international safety standards to help your equipment achieve safe and stable operation. Choosing World Known Precision Industry will give your industrial products a reliable braking protection.