What is Casting? 5 Types of New Casting Technology
Casting is a manufacturing process wherein high-temperature liquid metal is poured into a mold cavity, allowed to solidify, and then the casting is removed. According to data surveys, the top three materials in global casting production are gray cast iron, ductile iron, and aluminum, accounting for 85% of the total. Among them, gray cast iron and ductile iron together account for 71%, indicating significant demand in the cast iron market.
Sand casting technology is widely employed and represents one of the earliest casting methods developed. It remains the primary technology for producing iron castings. The utilization of sand as a mold material entails relatively low costs. Considering factors such as casting size, quantity, and cost, sand casting emerges as a viable and economical casting solution.
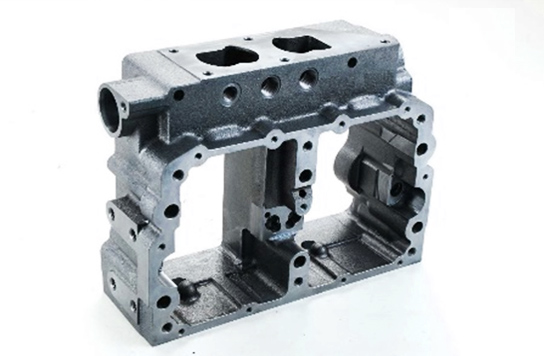
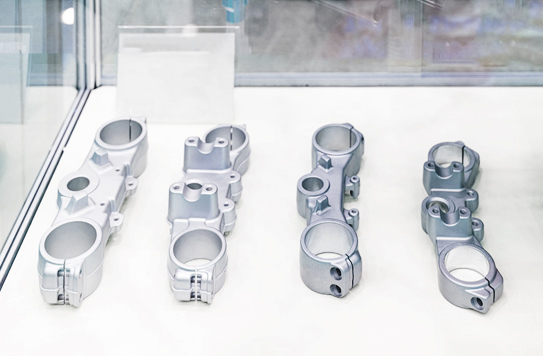
With a focus on enhancing casting quality, new casting methods have emerged to address defects caused by poor flow. These methods include::
- Vacuum die casting: This technique involves installing an air extraction device on the mold to evacuate air from the mold, reducing pores caused by trapped air.
- Laminar flow die casting: This method modifies the traditional high-speed filling of die-casting to a lower speed, reducing the amount of air entrapped during the filling process.
- PF die casting (Pore-Free Casting): Also known as porous die casting or oxygenated die casting, this approach involves injecting oxygen into the mold before filling to minimize air entrainment.
- GF die casting (Gas-Free Casting): This method expels excess air through exhaust holes in the mold, akin to vacuum die casting.
- Squeeze Casting: This technique combines die casting and forging principles, wherein low-pressure casting is initially performed followed by the application of high pressure to produce die-casting parts with fewer defects and greater strength.
These aforementioned methods aim to address flow-related issues, each offering various improvements. Consequently, they have led to the development of advanced manufacturing techniques such as ultra-high-speed die casting, high-vacuum die casting, and semi-solid casting. These approaches build upon speed, air extraction, and semi-solid casting principles, respectively, further advancing shaping capabilities. Notably, semi-solid casting combines the benefits of casting and forging and can be categorized into thixocasting and rheocasting based on different processes.
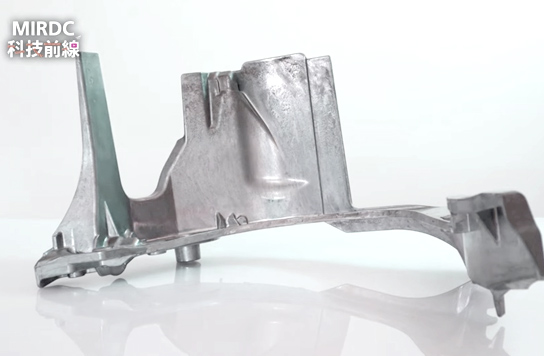
Since the inception of casting technology, efforts have not only been directed towards enhancing existing technical foundations but have also extended to more innovative realms such as materials and gigacasting technologies, thereby propelling casting technology to new heights. Current technological developments include:
Grain Technology: Common casting defects such as shrinkage cavities and pores can be addressed not only through the aforementioned casting technologies but also by focusing on casting grain refinement. Fine-grain casting technology involves controlling casting parameters, applying mechanical external force, or incorporating grain-refining agents to refine casting grains, thereby enhancing mechanical properties.
Gigacasting: Single-piece die-casting, pioneered by Tesla, has spurred other automotive manufacturers to invest in this technology. The adoption of integrated molding in the automotive industry not only boosts production efficiency but also streamlines the production process and components.
In conclusion, since the inception of casting technology, advancements have been made in various aspects, ranging from cost efficiency and quality improvement to sustainable development and waste reduction. Technologies have evolved toward reducing production costs and enhancing the quality of castings.
WKPT utilizes mature in-house sand mold casting technology, complemented by DISA automated modeling and MAGMA software-assisted analysis. Additionally, WKPT has developed high-strength ADI materials, facilitating the application of cast iron parts in transportation, construction machinery, agricultural machinery, and other sectors. In the casting application of non-ferrous metals, WKPT offers aluminum alloy gravity casting, die-casting, investment casting, and other mechanical parts through diversified supply chain resources. WKPT has achieved notable success in aviation, medical equipment, and high-precision equipment applications. In addition to metal forming, plus machining, and surface treatment processes, this comprehensive approach represents WKPT’s OEM manufacturing solution for mechanical components across various industries.
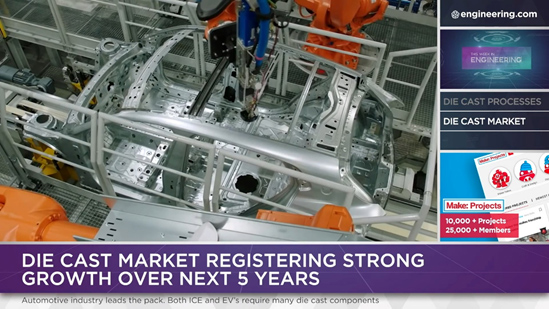