Improvement In Metalworking with CATIA
CATIA was developed in the 1980s by French software design company Dassault Systèmes S.A. It was originally used for aircraft manufacturing and later expanded to other product design applications, including automobile, vessel, and other consumer goods. With technology developing, the application of CATIA has been spread to the aviation, national defense, transportation, high technology, industrial equipment, construction, and biomedical industries.
In our precision metalworking solutions, CATIA will be used in the stages of metal rapid prototyping, tool development, and machining processes. Before being imported into CATIA, it was programmed by engineers for machining. Before CATIA was introduced, our engineers needed to do programming for machining. However, manual programming not only takes a long time but also has practical limitations such as curved surface programming. In order to improve design efficiency and reduce limitations, we have imported CATIA CAD/CAM, which can directly do programming through the software and converted into a machining program, greatly reducing the time and limitations of manual programming.
-
Improve programming efficiency:
The tool processing path can be simulated through CATIA CAD/CAM to speed up the programming efficiency and time. For example, a program that requires one week of working time can be reduced by more than 50% time with the assistance of CATIA, depending on the design complexity. -
Improve machining accuracy:
Using CATIA can foresee possible errors such as overcutting or collisions through the CATIA NC tool simulation function, which can prevent program errors and improve machining accuracy. -
Validate the quotation in advance:
The CATIA's simulation function not only brought the aforementioned improvements but also knew the actual machining time in advance, which can verify the accuracy and correctness of the quotation cost in advance.
CAD/CAM is widely used in precision metalworking, especially in the complicated machining process of fully engraved parts and aluminum alloy housing. By checking the tool path on CATIA, the optimized path can be calculated, and shortened the actual machining time. In addition to the assistance for on-site machining, our R&D engineer commented that CATIA has an irreplaceable advantage in design changes. Through the real-time simulation of variation analysis, differences can be quickly identified and generate relevant data for product analysis.
The engineer also pointed out, "We can connect and inherit the processes of 2D/3D drawing, assembly, and CAM in CATIA, and it successfully saves our work time a lot.”
In the future, CATIA will not only be used in product design and machining but also expanded to production molds and machining fixtures. It can provide feedback on the client's design through the clamping analysis, reflecting the rationality of workpiece forming and reducing the instability of the clamping greatly. Through the application of CATIA, we have improved our own capabilities of machining and design, providing the clients with more comprehensive precision metalworking service.
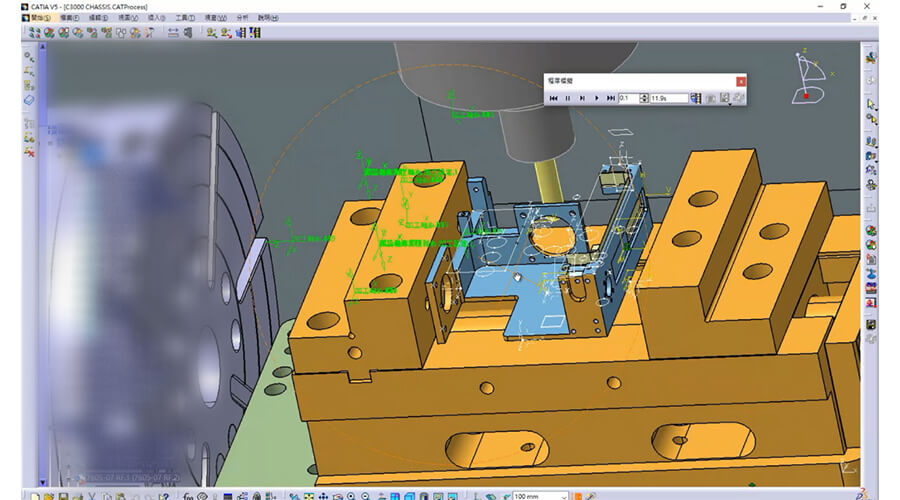