Aluminum Alloy Rust Resistance & Advanced Anodizing Technology in Modern Industries
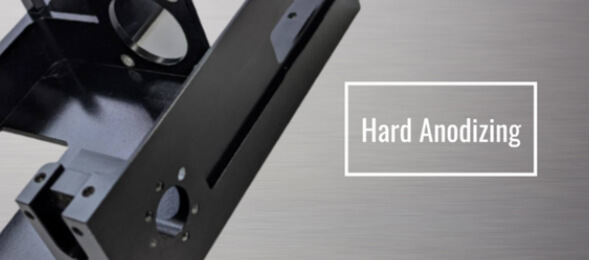
Aluminum alloy is an active metal that generates an oxide film when exposed to air, isolating the metal surface from environmental oxidation. However, this naturally generated oxide film may still corrode over time when exposed to the external environment. To protect the surface of aluminum alloy, anodizing is often used to generate a thicker protective film artificially, thereby enhancing the surface hardness and corrosion resistance of the aluminum alloy.
For example, for the 6061T6 aluminum alloy casing used in the manufacture of medical testing equipment, hard anodizing is typically employed. Compared to regular anodizing, hard anodizing generates a thicker protective film, thereby producing better surface hardness and corrosion resistance. To conduct hard anodizing, various parameters such as temperature, voltage, and current density need to be adjusted to form a 25µm thick protective layer with a hardness of HV500 on the surface of the aluminum alloy. This protective layer meets the ISO10074 standard for anodizing aluminum alloys.
In many industrial applications of aluminum alloys, medical settings, in particular, require lightweight, high-strength, and acid-alkali-resistant testing equipment. Therefore, we are committed to assisting customers in producing higher-quality aluminum alloy testing equipment. One of our successful projects is the production of 6061T6 aluminum alloy casings with hard anodizing to ensure that their surfaces have sufficient hardness and corrosion resistance.
Anodizing aluminum alloys is a widely used surface treatment technique. In addition to its important application in medical testing equipment, anodizing aluminum alloys is also a critical surface treatment technology in the aviation and aerospace industries. Aluminum alloys are commonly used as structural materials for aircraft, and the corrosion resistance and anti-corrosion properties of aluminum alloys directly affect the safety performance of aircraft. Improving the corrosion resistance of aluminum alloys can also increase their surface hardness and friction performance, thereby enhancing their service life in extreme environments.
Secondly, aluminum alloy anodizing is widely used in the manufacturing of transportation tools such as automobiles, trains, and ships. Anodizing not only improves the hardness and corrosion resistance of the aluminum alloy surface but also increases its appearance and durability, reducing the impact of wear and corrosion on the vehicle's exterior. In addition, aluminum alloy anodizing is also widely used in fields such as electronics, optics, and construction. For example, in electronic products, anodizing can improve the conductivity and wear resistance of the aluminum alloy, increasing the product's lifespan. In optical products, anodizing can improve the reflection and scattering performance of the aluminum alloy surface, enhancing the product's optical performance. In the construction field, anodizing can enhance the durability and corrosion resistance of aluminum alloy products, increasing their lifespan and aesthetic appeal.
In any case, aluminum alloy anodizing has important applications in many industries. It not only improves product performance and quality but also increases product lifespan and reduces maintenance costs. Therefore, it holds a very important position in modern industrial production.
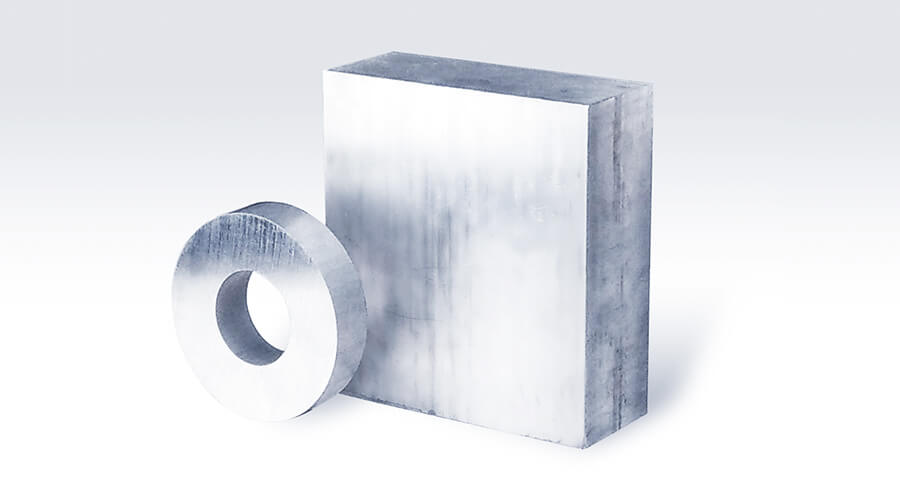