Visual Inspection Meets AI: The Future of Quality Control in Metal Manufacturing
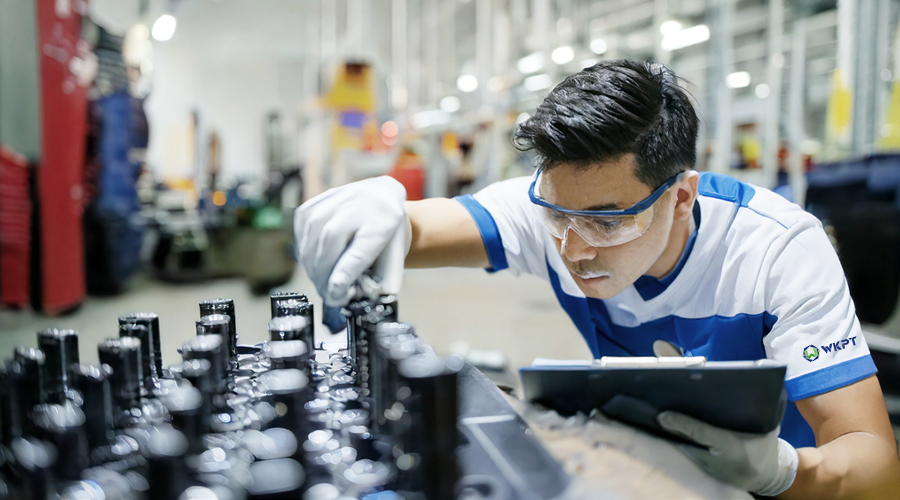
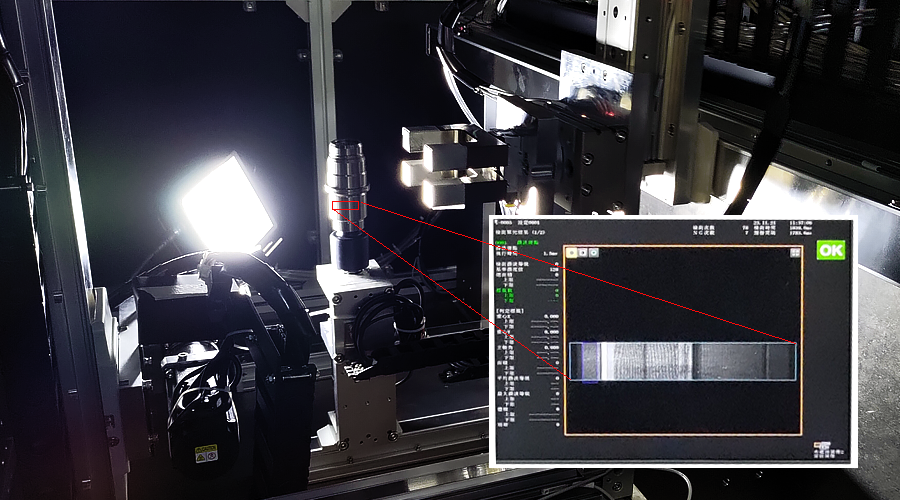
In today,s metal component manufacturing industry, quality control has become more crucial than ever. As products grow increasingly complex and customer expectations soar, manufacturers are turning to advanced visual inspection and smart technologies to ensure top-notch quality.
For centuries, visual inspection has served as the animating principle behind quality control of metal component manufacturing processes. Experienced inspectors inspect all parts carefully to find defects and measure dimensions. But as production volume increase, manual inspection will show its limitations:
- ●Human error:Even experienced inspectors can make mistakes, missing defects or misclassifying parts.
- ●Fatigue:Long hours of repetitive inspection tasks can lead to decreased attention and accuracy.
- ●Inconsistency:Different inspectors may have varying standards, leading to inconsistent quality assessments across shifts or production runs.
- This can all make way for missed defects or false rejects, plus costly errors and unhappy customers.
Machine vision A unique and revolutionary way for quality control The system combines high-resolution cameras, advanced image processing software and machine learning technology to analyze components with accuracy and in less time. The benefits of machine vision in defect detection are game-changing:
- ●Unrivalled Accuracy:Detect defects down to a fraction of millimeter
- ●Consistency:24/7, continuous and stable test results
While the benefits of machine vision and smart inspection technologies are clear, implementation requires careful planning. Key considerations include:
- ●Assessing Compatibility:Begin by evaluating your existing production lines and processes to identify potential bottlenecks or constraints.
- ●Planning for Integration: Develop a phased implementation plan with clear milestones and timelines.
- ●Investing in Training: Provide comprehensive training for operators and technicians to ensure they can effectively use and maintain the new technologies.
WKPT, a leading manufacturer of metal components for commercial vehicles, successfully implemented advanced smart image recognition technology on cast iron parts. This AI-powered system automatically identifies and classifies various surface defects, including sand holes, shrinkage cavities, and slag inclusions. After implementation, WKPT saw significant improvements:
- ●Increased Inspection Efficiency
- ●Production Line Optimization
Learn more:Digital Transformation in Progress - The Smart Manufacturing Journey of WKPT
Visual inspection enhanced by AI and smart technologies is reshaping quality control in metal component manufacturing. By combining the precision of machine vision with human expertise, manufacturers can achieve unprecedented levels of quality and efficiency. In the era of Industry 4.0, Quality 4.0 has emerged in response, representing a shift in quality control thinking to keep pace with the technological advancements of Industry 4.0. Quality 4.0 is not limited to adopting new technologies, but emphasizes integrating new technologies to improve quality, and understanding the importance of people and processes in the digital transformation journey.
The transition from manual visual checks to smart technologies has completely transformed the way we ensure quality in manufacturing metal components. Here at WKPT, we have fully embraced this transformation by incorporating advanced image recognition systems that greatly enhance our inspection procedures. This decision shows our dedication to meeting the changing demands of customers and remaining leaders in manufacturing excellence. Are you in search of a supply chain partner who blends expertise with state of the art technology? Get in touch with us to discover how our advanced quality control methods can add value to your projects. Let's craft products that meet the high standards of today while preparing for the challenges of tomorrow.
Learn more:Looking for a manufacturing partner that can meet future challenges? Explore WKPT’s services now