Carbon Emission Reduction Through Smart Process Optimization
Global trends indicate that environmental protection has become a universal value, with countries worldwide recognizing the importance of energy conservation and carbon reduction. In response to the demand for a global green supply chain, international regulations on carbon emissions have gradually been established. In adapting to the requirements of the global supply chain, WKPT initiated the "Production Process Upgrade with Smart Manufacturing for Automotive Component" project in 2023. This project aims to enhance the application of networking technology in the precision machining centers. Through process optimization, it assists in the analysis of component manufacturing processes while utilizing a carbon emission model to predict the potential carbon emissions generated during processing.
WKPT utilizes force mechanics simulations in accordance with cutting processes to estimate parameters at each point along the tool path. This includes chip thickness, cutting force, spindle load, and tool load. Based on the simulation results and user-defined condition limits, the feed rate is adjusted to achieve effective protection of the spindle, tool, and workpiece.
WKPT utilizes metal cutting dynamics under specific conditions. By setting parameters such as maximum chip thickness, lateral cutting force, axial cutting force, spindle torque and air cutting, the optimal cutting feed efficiency is adjusted based on condition limits. Through further optimization using the cutting force mechanics analysis module, the machining programs are diagnosed, machining feed rates are modified, and ultimately, optimized machining programs are generated. This process effectively enhances machining efficiency, reduces carbon emissions, and protects the spindle, tools, and workpieces.
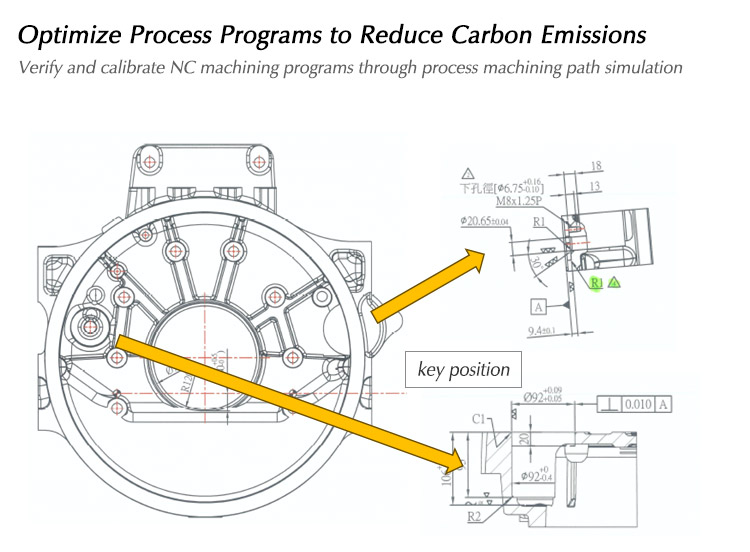
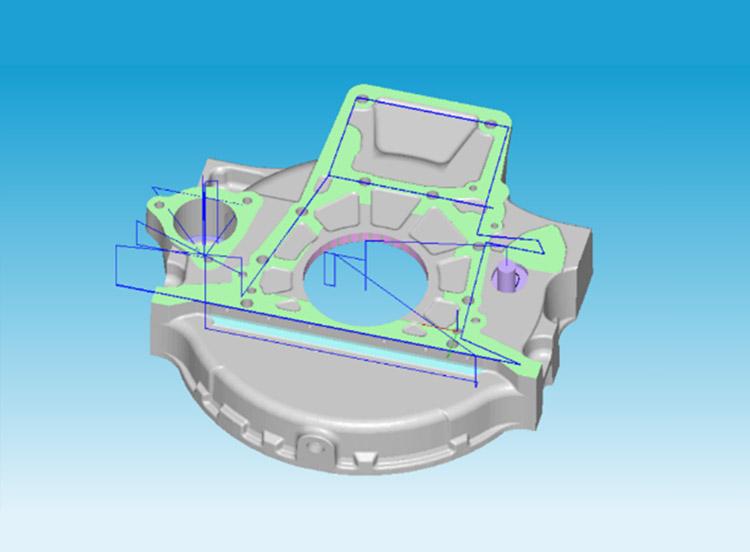
WKPT’s process optimization is based on cutting force mechanics analysis. It involves analyzing the processes, workpieces, and machinery used in milling process optimization, calculating the forces exerted on the tools due to material removal. Based on conditions such as machining paths, workpieces, and machinery, the optimal feed rates are set to enhance cutting efficiency, reduce unnecessary power consumption, thereby saving processing time and lowering carbon emissions. The specific steps include:
- Conducting a simulation of the machining path to estimate data such as chip thickness and cutting force.
- Inspecting and calibrating NC machining programs to ensure machining accuracy.
- Using 3D simulation software to inspect the final shape after material removal.
- Setting cutting parameters based on the results of cutting force mechanics simulations.
- Optimizing through the cutting force mechanics analysis module, adjusting machining feed rates.
- Generating optimized machining programs.
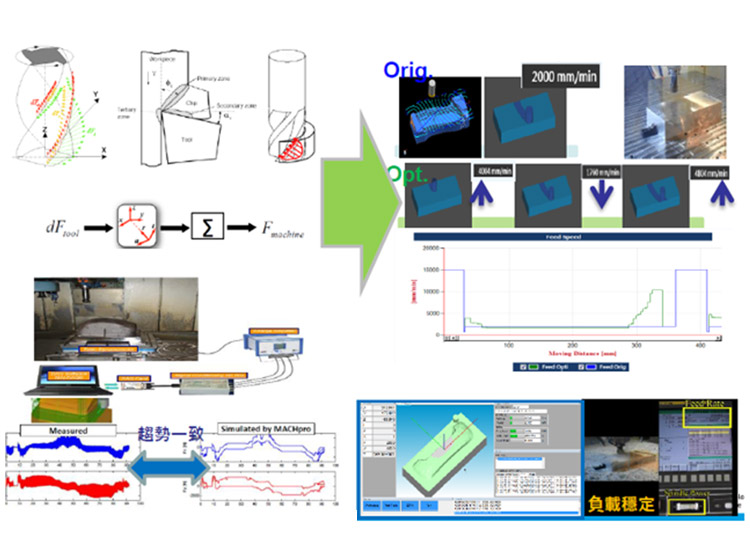
In cutting force mechanics simulations for the manufacturing process of automotive components, WKPT estimates chip thickness, cutting force, spindle load, and tool load at each point along the tool path. For certain NC programs with insufficient load, adjustments to the feed rate are made to increase the load, achieving optimization and enhancing process efficiency.
At the same time, adjusting the increase in chip load and limiting the lateral load, adjusting the cutting feed rate based on the force situation, to achieve the goal of improving cutting efficiency.
Through practical testing, WKPT’s optimized processes has saved 5-30% of processing time, reduced power consumption by approximately 0.8-4.7 degrees, decreased carbon emissions by about 6.78%, and simultaneously increased production efficiency by 19.52%. WKPT not only meets the requirements of the international supply chain but also demonstrates a commitment to environmental sustainability.
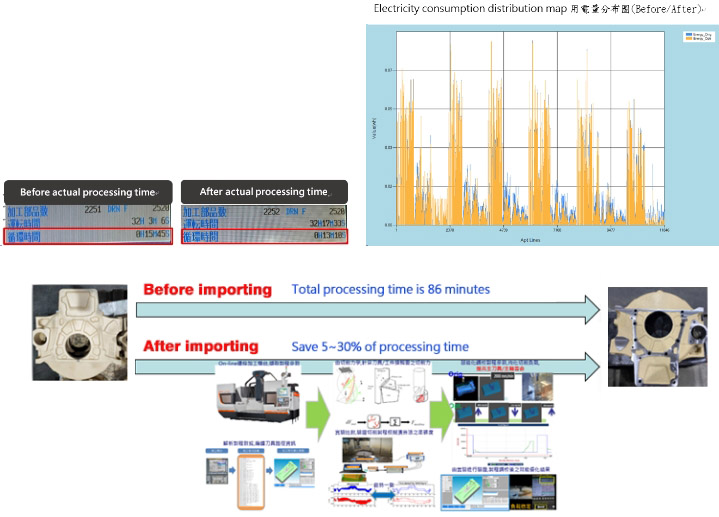