Application of reverse engineering in modern mechanical parts manufacturing
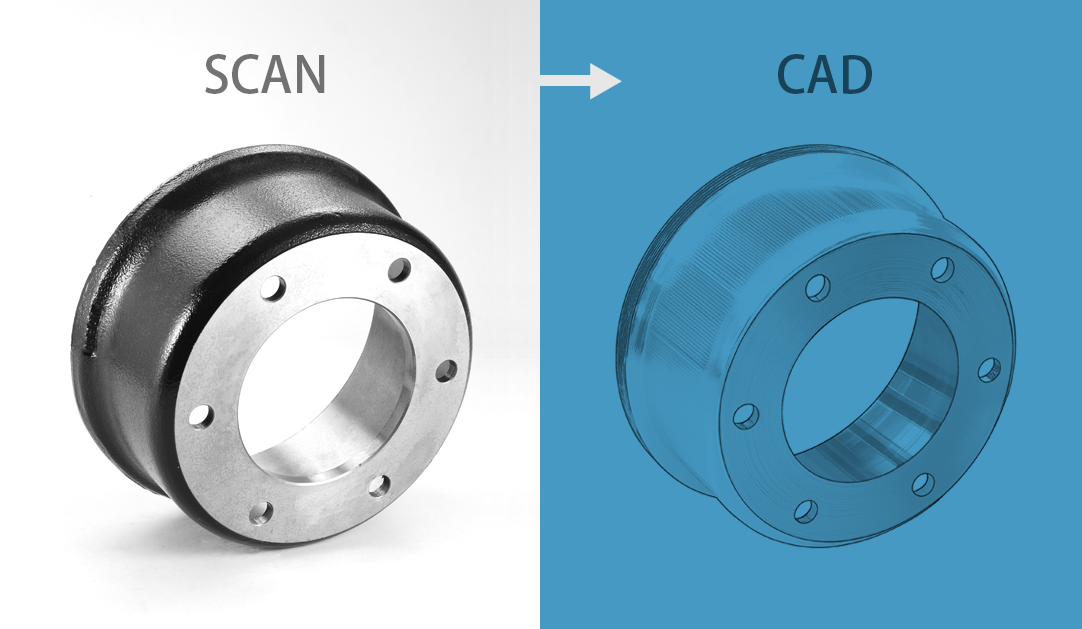
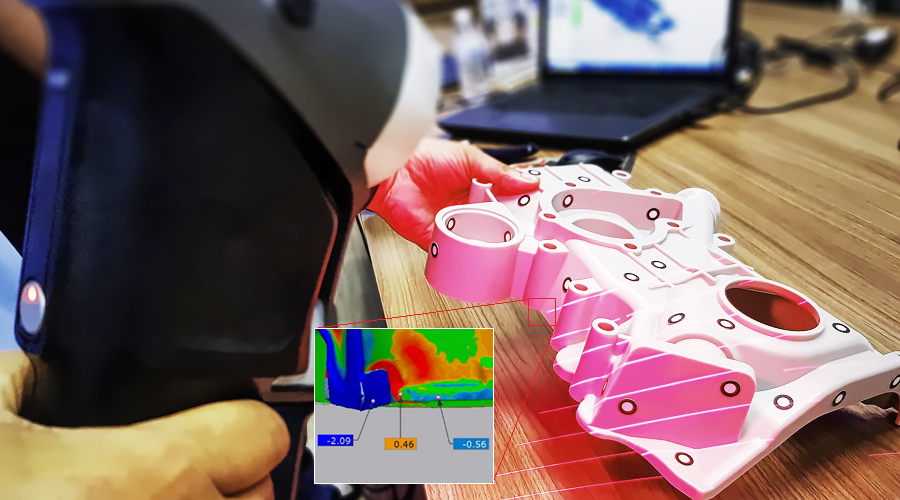
When it comes to product development, people often envision starting with a sketch, followed by creating drawings, designing based on the drawing's requirements, generating molds, verifying them, and ultimately producing finished products. This type of product development process, which starts from scratch, is called forward engineering. Conversely, when you work backward from a finished product to create drawings and designs, this type of development process is called reverse engineering. Depending on the needs of product development, both forward and reverse engineering can be suitable at different times.
Due to its properties of reversibility and non-destructiveness, reverse engineering is suitable for product development situations lacking drawings or for verifying existing design drawings. Reverse engineering can assist product developers in creating design drawings or verifying whether the product conforms to the expected design. It is commonly utilized across various fields including computer engineering, mechanical engineering, electronic engineering, software engineering, and chemical engineering.
The process of reverse engineering can be divided into three steps: Information Extraction, Modeling, and Review. To perform information extraction in reverse engineering on a mechanical component, it is necessary to prepare 3D scanning equipment to obtain the overall shape information in the form of grid data, typically saved in the STL (Stereo Lithography) format. However, the STL grid data cannot be directly used; it needs to be converted into an STP file format suitable for modeling. Based on this, the CAD model of the mechanical components should be established. Finally, a review is conducted to confirm that the model aligns with the original design of the mechanical component and is suitable for subsequent product development.
WKPT has extensive experience in reverse engineering, utilizing this technology to drive product development across various fields, including propulsion components, power system components, and pipeline system components. WKPT has successfully aided clients in completing the entire metal product manufacturing process, encompassing product development, molding, machining, and surface treatment, even in cases where no sketches were initially available.
As mentioned previously, the reverse engineering process initiates with information extraction, followed by the creation of a model from the obtained scanned mesh data. Given the variability in object surface morphology, obtaining a validated surface model is considered a crucial aspect of reverse engineering. Users must possess proficiency in 3D drawing software like Pro/ENGINEER or SolidWorks. Furthermore, the construction method of the model may differ among users, and if disparities exist in the models constructed by different users, both parties must engage in discussions regarding the construction method to comprehend each other's approaches and achieve a consensus.
In situations where original CAD design drawings are unavailable, employing reverse engineering techniques on physical objects can alleviate the challenges associated with product development in the absence of design drawings and validate the product design. In markets characterized by small and diverse product demands, reverse engineering can aid in reducing the product development cycle, enabling companies to efficiently deliver products to target markets. WKPT specializes in precision metalworking and maintains a comprehensive track record of product development through reverse engineering. If you are seeking suitable metalworking services, we invite you to explore our services further.