Abnormal parts processing!!! RCA-Root Cause Analysis Application Example
What is Root Cause Analysis?
Root Cause Analysis (RCA), also referred to as RCA analysis or root and cause analysis, is a structured approach used to pinpoint the underlying reasons behind issues in manufacturing processes. Diving beyond surface level problem solving, RCA aims to tackle problems at their core. The concept of root cause revolves around understanding the fundamental cause of an issue's origin. In industries like machining where efficiency and quality are top priorities, RCA plays a vital role in driving continuous improvement. By focusing on identifying root causes, RCA empowers manufacturers to implement tailored solutions that reduce problem recurrence and elevate overall manufacturing standards.
Common Root Cause Analysis Methods
- 5 Whys (also known as Five Whys): Involves repeatedly asking "why" to dig deep into the root of the problem. The 5 whys root cause analysis is a simple yet powerful technique.
- Fishbone Diagram (Ishikawa Diagram): Also called fishbone analysis, this method visually categorizes potential causes of problems, covering aspects such as personnel, processes, materials, and environment.
- 4M1E Method: Analyzes problems comprehensively from five angles - Man, Machine, Material, Method, and Environment.
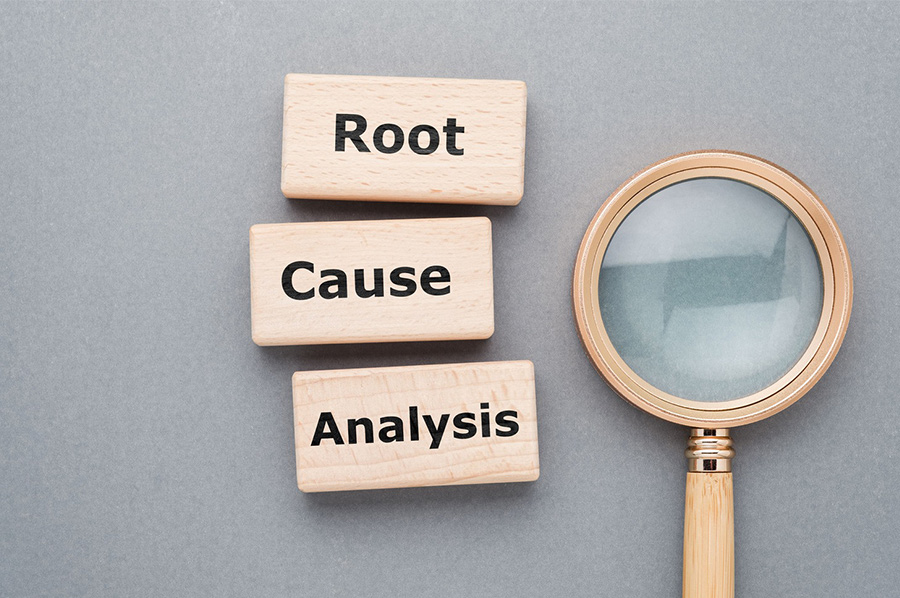
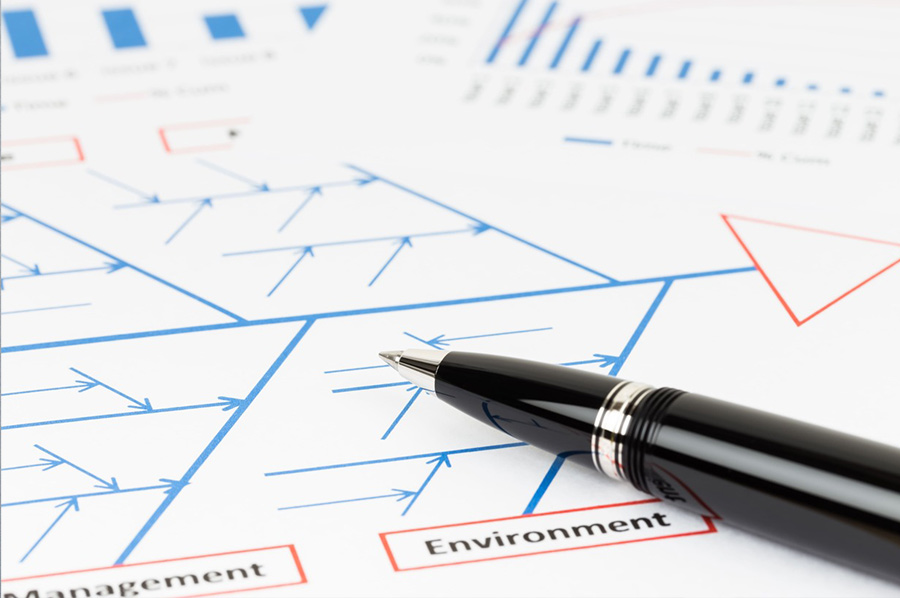
The Root Cause Analysis Process
The root cause analysis methodology typically follows five steps:
- Identify Problem: Clearly define the problem and assess its impact on production.
- Data Collection: Gather comprehensive data from sources such as equipment logs, quality control reports, and personnel feedback.
- Identify Potential Factors: Use techniques like the 5 whys or fishbone analysis to explore various possibilities.
- Determine Root Causes: Conduct in-depth analysis of identified factors, potentially involving hypothesis testing. This step is crucial for root cause identification.
- Implement Solutions: Develop and execute solutions targeting the root causes.
By following this systematic approach, manufacturing teams can effectively solve problems in their processes, thereby improving manufacturing efficiency and quality.
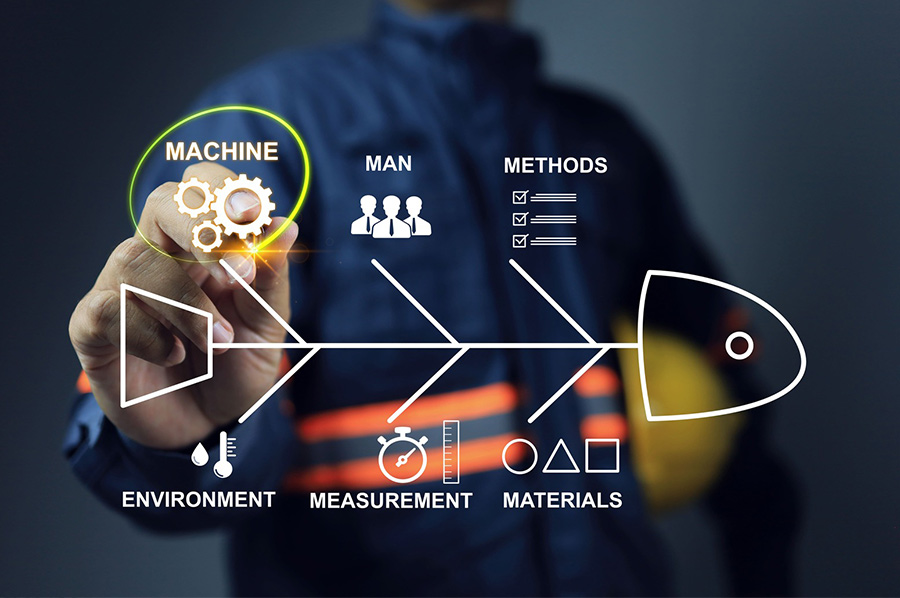
Root Cause Analysis Applications in Machining
WKPT discovered abnormal tool vibration during a machining process and immediately initiated a root cause analysis. The team employed the 4M1E method to comprehensively investigate the causes of the problem. This serves as one of many root cause analysis examples in the manufacturing sector. Based on the investigation results, the company designed and implemented a complete solution:
- Man: Developed specialized training programs for operators, packaging staff, and quality inspectors to enhance their ability to detect and respond to tool vibration issues.
- Machine: Established a detailed regular equipment maintenance plan, focusing particularly on the condition of the turret precision, hydraulic system, and clamping mechanism.
- Method: Revised process documents, incorporating specific vibration checks into key instructions and inspection forms, ensuring clear inspection criteria at every stage.
- Material: Implemented more thorough cleaning procedures during mold and line changes to reduce residues that might cause vibrations.
- Environment: Equipped Quality Assurance (QA) staff with endoscopes for more detailed cutting trace inspections.
Through the implementation of the 4M1E root cause analysis method and corresponding improvement measures, WKPT not only prevented the recurrence of tool vibration issues but also enhanced overall machining precision and product quality. This application of root cause analysis demonstrated WKPT’s systematic problem-solving capability when facing manufacturing challenges.
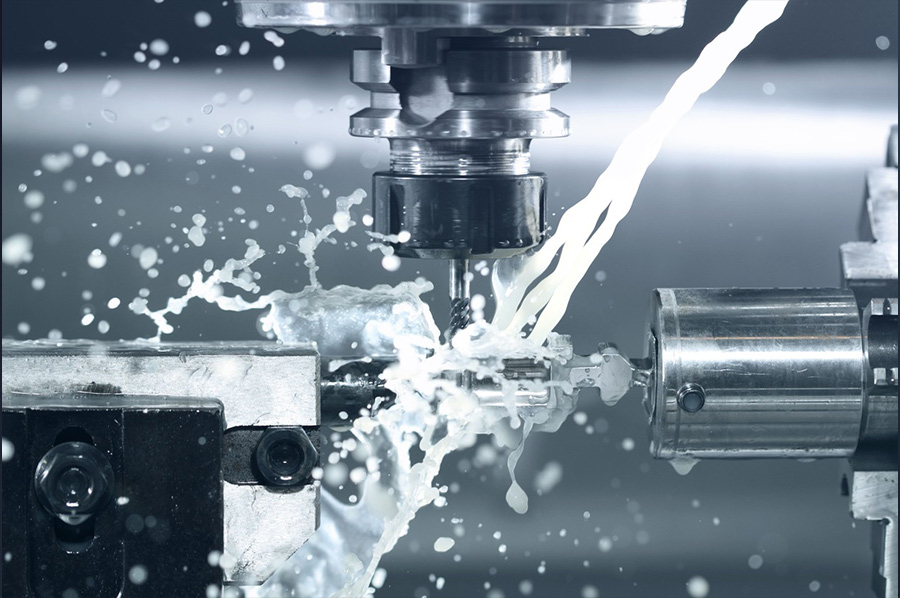
Conclusion
Root Cause Analysis (RCA) plays a crucial role in problem solving within the manufacturing industry. By utilizing structured approaches like the 5 Whys, Fishbone Diagram, and 4M1E, companies can deeply investigate the root causes of issues instead of just treating surface level symptoms. The success story of WKPT highlights how RCA proves its worth in real world scenarios. Through thorough analysis and practical adjustments, the company not only fixed the tool vibration problem but also enhanced the overall quality of their manufacturing process. This has enabled us to deliver more dependable production services for metal components to you.